5 common packaging challenges and how automation solves them
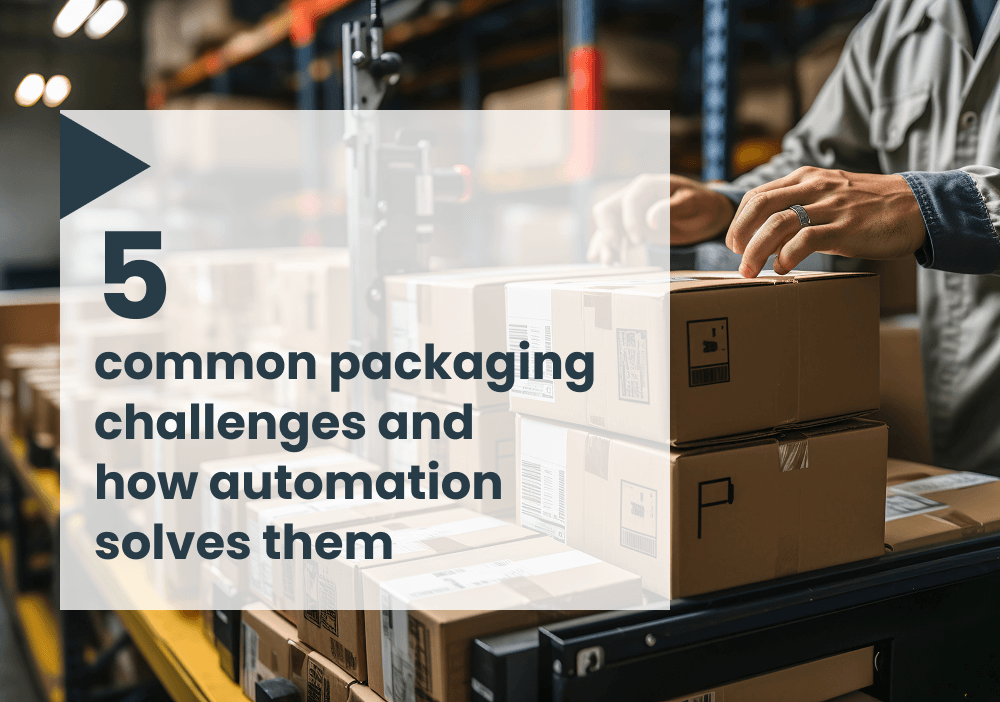
Packaging may seem like a straightforward process, but for many small and medium-sized businesses, it’s a daily struggle filled with inefficiencies, errors, and lost productivity. When packaging processes are manual, mistakes happen — products are mislabeled, improperly sealed, or inconsistently filled. These mistakes aren't just inconvenient; they can lead to dissatisfied customers, wasted materials, and financial loss.
For businesses looking to grow, the demands of scaling can expose even more gaps in their packaging workflow. Increased order volumes often lead to overworked employees, slower production times, and rising operational costs. In a highly competitive market, these issues can make or break a business.
With the right automated filling equipment, automatic sealing machine, and label applicator, businesses can enhance their packaging speed, accuracy, and consistency. At Cleveland Equipment, we specialize in providing economically priced semi-automated packaging systems designed to help small and medium-sized businesses overcome these common packaging challenges.
5 common packaging challenges
For small businesses, every dollar and every minute counts. Investing in semi-automated packaging equipment can provide a significant return on investment (ROI) by reducing manual labor, minimizing waste, and increasing output. Here are some key benefits:
1. Inconsistent fills
One of the most frequent packaging issues is inconsistent filling, especially for businesses that rely on manual processes. Whether you're filling bottles, containers, or pouches, achieving the correct fill level can be challenging without the right equipment.
Manual filling often leads to overfilling or underfilling, resulting in product waste, customer complaints, and potential compliance issues. For businesses in the food, beverage, and cosmetic industries, inaccurate fills can lead to costly product recalls or fines.
Imagine a small skincare company that hand-fills its products. With fluctuating fill levels, some jars end up with too much product, increasing costs, while others are underfilled, leaving customers dissatisfied. These discrepancies not only hurt the bottom line but also damage brand reputation.
Inconsistent fills can also disrupt inventory management. When products are not accurately filled, it becomes difficult to track inventory, forecast needs, and maintain quality control.
2. Slow labeling processes
Manual labeling is not only time-consuming but also prone to errors. Crooked, misplaced, or bubbled labels make products look unprofessional, leading to negative customer impressions. Small businesses often rely on staff to manually apply labels, a process that can lead to fatigue and errors over time. Additionally, applying labels by hand limits production speed, making it difficult to scale when demand increases.
For example, a local coffee roaster may struggle to keep up with labeling demands during peak seasons. Without an efficient system, they risk shipping products with incorrect or missing labels, causing potential compliance issues.
Slow labeling can also delay shipping schedules, creating backlogs in production lines and leading to dissatisfied customers waiting for their orders.
3. Poor seals and packaging integrity
Packaging integrity is essential for product protection and consumer safety. Manual sealing, however, is often inconsistent, leading to poor seals that compromise product quality.
A manual approach to sealing can result in loose or incomplete seals, increasing the risk of product spoilage, contamination, and damage during transit. This is particularly concerning for businesses in the food and beverage industry, where proper seals are essential for product freshness.
Inadequate seals can also lead to product returns and refunds, straining customer relationships and hurting profitability. For businesses trying to expand into retail or wholesale, inconsistent sealing can prevent them from meeting retailer standards.
4. Manual errors and human fatigue
Human errors are inevitable when packaging processes are entirely manual. Employees become fatigued, distracted, or rushed, leading to mistakes like incorrect labeling, misfilled containers, or poorly sealed packages.
Mistakes in manual processes can be costly — from incorrect product labeling to accidental product damage. These errors not only waste materials but can also lead to regulatory fines, especially for businesses dealing with sensitive or regulated products.
Relying heavily on manual labor can result in inconsistent product quality, creating issues for businesses trying to establish a reliable brand presence.
5. Difficulty scaling production
As businesses grow, manual packaging processes can become a bottleneck. Increased order volumes can overwhelm a team, slowing down production and increasing the likelihood of mistakes.
For a small eCommerce business experiencing growth, scaling production without sacrificing quality or speed can be a challenge. Manual processes often struggle to keep up, resulting in missed deadlines, dissatisfied customers, and missed revenue opportunities.
Scaling requires investments in equipment and technology that can accommodate increased demand while maintaining quality and consistency.
5 packaging solutions: how automation solves these challenges
“We have been so happy with our new filling line. It has already paid for itself! It has literally cut our production time in half!" - Brandon R.
1. Automated filling equipment
Equipment like piston fillers and liquid packaging equipment, address inconsistent fills by providing precise, repeatable filling volumes. With advanced settings for speed and accuracy, businesses can maintain product quality while reducing waste.
2. Label applicators
A label applicator simplifies and speeds up the labeling process, ensuring accuracy and consistency. By investing in a label applicator from Cleveland Equipment, businesses can achieve professional-grade labeling at a fraction of the cost.
For businesses like cosmetics manufacturers, a bottle labeling machine eliminates labeling errors, improves product presentation, and ensures compliance with industry standards.
3. Automatic sealing machines
An automatic sealing machine ensures airtight, consistent seals, reducing the risk of product spoilage, contamination, and returns. With this contactless method, staff time is freed up to focus on other tasks. Induction sealers provide foil seals under a cap for plastic and glass containers. This process extends shelf life for your product, preserving freshness and preventing the possibility of leaks.
4. Shrink wrapping machines and heat tunnels
A heat tunnel for shrink sleeves provides a tamper-evident, secure package that enhances product appearance and protection. Businesses can maintain consistent packaging while minimizing labor costs and material waste.
5. Box machines and carton sealers
For businesses scaling production, box machines and carton sealers improve packaging, reduce manual labor, and eliminate bottlenecks. These systems integrate easily into production lines, enabling faster, more efficient packing and shipping.
"We purchased the
... it increased our productivity by 38%! It also reduced our staffing hours and allowed us to rearrange our employees for other tasks. I recommend this case erector to any small business just starting." -Chad M.Get started today
At Cleveland Equipment, we understand the packaging challenges businesses face. Our economically priced, semi-automated packaging systems are designed to help you scale smarter, faster, and more profitably.
Request a quote and discover how our solutions can revolutionize your packaging process!