Are you wasting money on manual packaging?
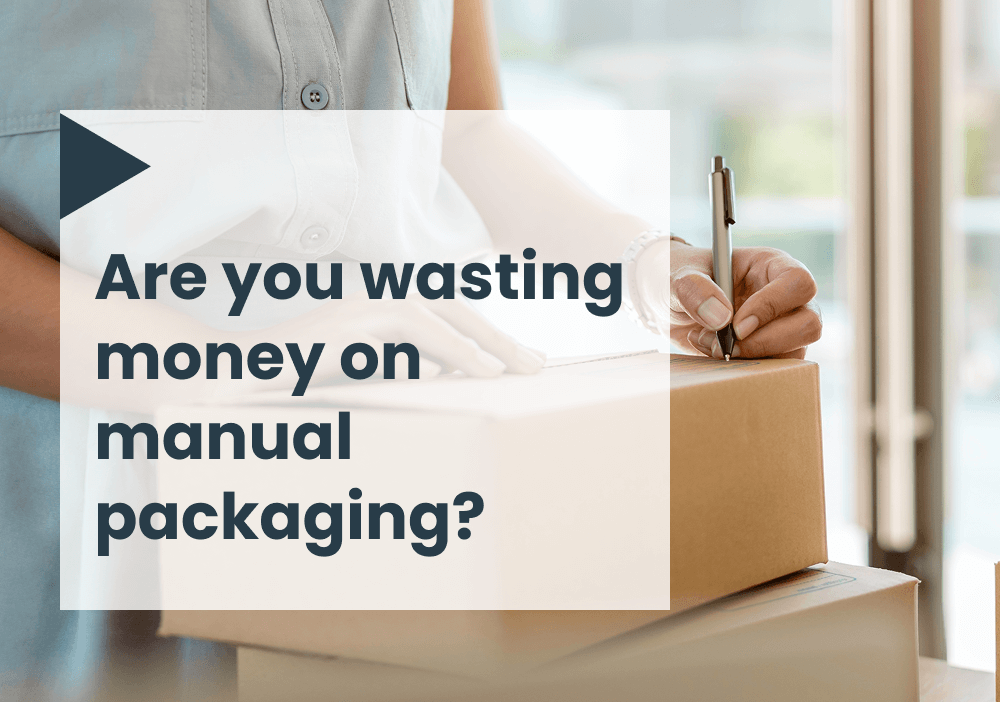
For many small and medium-sized businesses, manual packaging feels like the only option. Hand-labeling bottles, taping boxes, and manually filling containers might seem cost-effective, but in reality, these processes drain valuable time and resources. Slow production speeds, inconsistent results, and human errors all contribute to higher long-term costs.
Investing in semi-automated packaging solutions can dramatically cut labor costs, boost efficiency, and reduce waste. With affordable options available, businesses can scale faster without breaking the bank. Whether you run a mom-and-pop shop or a growing operation, upgrading to semi-automated equipment ensures your team focuses on what truly matters: serving customers and growing your business.
If manual packaging is eating up your time and profits, it’s time to rethink your approach. Semi-automated solutions pay off both short- and long-term.
The ROI of semi-automated packaging solutions
Switching to semi-automated packaging might seem like a large upfront investment, but the return on investment (ROI) far outweighs the costs. Here’s why:
1. Lower labor costs
Manual packaging is labor-intensive. Employees spending hours taping boxes, filling bottles, or applying labels could be focusing on other revenue-generating tasks. By integrating equipment like a box machine or piston filler, businesses significantly cut down on labor hours, reducing payroll expenses.
“We abuse this thing. I have been using it daily for a long time now. For the price, this is
” -Creative Specialty Foods2. Increased productivity
Consider a bottle filling equipment setup. Instead of employees painstakingly measuring and pouring liquids by hand, a liquid packaging equipment solution fills multiple containers simultaneously—at speeds no manual process can match. Increased output means more products ready for sale in less time, directly increasing revenue.
“The
fit right in with what we are doing and have made a huge difference in our output volume.” -Du Nord Craft Spirits3. Reduced product waste
Manual packaging errors—spills, overfills, and improper sealing—result in wasted product. Over time, these losses add up. Solutions like an automatic sealing machine ensure precision, minimizing costly waste and improving overall product consistency.
“We were hand sealing and this has
” -Cookies for Grown-Ups4. Consistency and reliability
Consumers expect uniformity in their purchases. If a label is crooked or a bottle is underfilled, it can create a negative perception of your brand. With a label applicator or carton sealer, businesses can ensure every product meets the same high standards, leading to better customer satisfaction and repeat purchases.
“Our
has worked well so far – we use it to apply labels to 5 products of varying sizes and shapes, and we have been able to apply labels in a consistent and high quality.” -Joy Organics5. Scalability without additional overhead
As demand for your product grows, manual packaging limits your ability to scale efficiently. Instead of hiring more employees or working longer hours, investing in Cleveland Equipment’s semi-automated solutions allows businesses to increase production capacity without increasing labor costs.
“We
from an average across all product lines from approximately 60 units per hour to approximately 320 units per hour. “ -ODW Logistics6. Long-term savings
The initial investment in a case sealer machine or heat tunnel for shrink sleeves might seem significant, but long-term savings in labor, waste reduction, and increased productivity quickly offset the costs. Many businesses see a full return on investment within months of implementation.
"We have been so happy with our new filling line. It has already paid for itself! It has literally cut our production time in half!" - Brandon R.
Manual packaging vs. semi-automated packaging: the financial benefits
- Speed and efficiency: Manual packaging is time-consuming. A team of employees taping boxes by hand will never match the speed of a box sealer machine. Semi-automated solutions allow businesses to double or even triple their output without adding staff.
- Error reduction and cost savings: Human error in manual packaging leads to wasted materials and rework. Crooked labels, overfilled bottles, or improperly sealed boxes can result in lost revenue. Equipment like a carton taper ensures accuracy and consistency, reducing errors and unnecessary expenses.
- Labor savings and employee satisfaction: Employees stuck doing repetitive packaging tasks often experience burnout. Automating processes not only saves money on labor but also allows staff to focus on higher-value tasks like customer service, marketing, and business development.
- Competitive advantage: Businesses that invest in semi-automatic equipment can meet customer demand faster, maintain high product quality, and reduce costs—allowing them to price their products more competitively and expand their market share.
Invest in our packaging solutions today
If your business still relies on manual packaging, you could be throwing money away every single day. The inefficiencies, labor costs, and wasted materials add up over time, limiting your ability to grow and compete. Investing in semi-automated packaging solutions—such as automated filling equipment, an automatic sealing machine, bottle filling equipment, and carton sealers—ensures you maximize profits, improve efficiency, and scale smarter.
Request a quote and learn more about our cost-effective, high-quality packaging solutions!